Optimized warehousing operations are crucial for efficient eCommerce fulfillment and increased customer satisfaction. They also help in keeping the costs low. When the operations are not optimized, inventory is not received or shipped on time, workers are not productive, and the business losses its customers and credibility in the market.
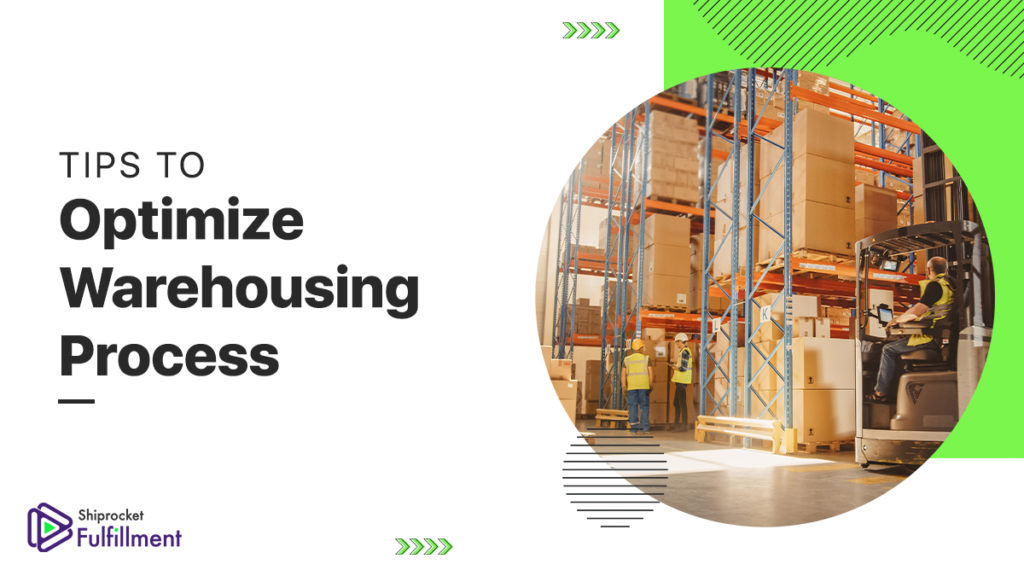
Optimizing the warehousing process means examining every aspect of the process, identifying inefficiencies, and working on them. The optimized warehousing process helps in accurate and on-time order processing and an efficient order fulfillment process.
This blog will help you understand the steps involved in the warehousing process and the best practices to optimize the operations.
Steps in Warehousing Process
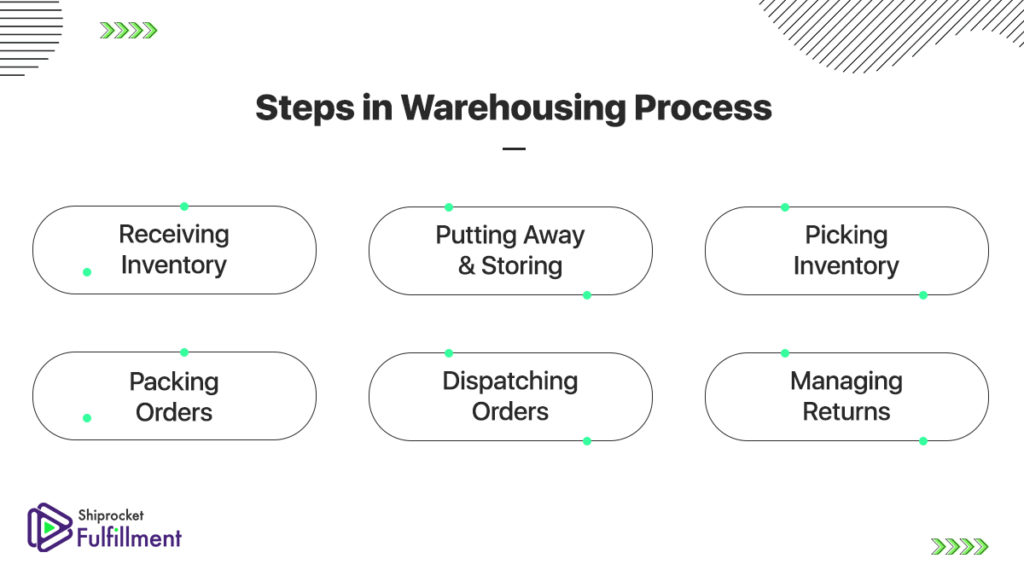
Fundamentally, there are six steps involved in the warehousing process – receiving inventory, putting it away, picking it, packing it, shipping it, and managing its return. Optimizing these steps will help you streamline your warehouse operations, reduce costs, and achieve better fulfillment operations.
Let’s take a look at the steps in the warehouse process and how to optimize them:
1. Receiving Inventory
Receiving inventory is the act of handling products and adding them to the warehouse system. The products can be as large as an air conditioner or as small as an awl pin. You may receive a single product and object or a pallet and crate.
Significantly, receiving is a crucial step in the entire warehousing process. To perform it properly, you should ensure that you have received the right product, in the right condition, and in the right quantity. If you fail to do it, it may have consequent impacts on your options.
Receiving inventory also means its responsibility is transferred to the warehouse. Therefore, you become accountable for maintaining its condition and quantity until it is shipped to the buyer. So, make sure you receive the products properly – this will reduce the chances of receiving damaged products. And its liability will also not fall on your shoulders.
Optimization Tip
The main objective of optimizing the inventory receiving step is receiving the load efficiently and avoiding the accumulation of different products at the receiving dock. You can have solutions like conveyer and power pallet trucks for efficient unloading of the cargo. This will also aid in clearing the receiving dock faster.
Alternatively, you can also use pallet and parcel dimensioners to automate the weight and dimension capturing. This will accelerate the receiving process.
2. Putting Away and Storing
Putting away the inventory is the second step in the warehousing process. Essentially, it is the movement of the goods from the receiving dock to their storage location. The put-away staff delivers the goods to the storage location. Once the goods reach the location, the operator either manually confirms or scans the bard code of the stock to confirm that it has reached the correct location. Once securely stored, the put-away staff confirms that the process is completed.
Optimization Tip
In the putaway process, the load is stored at its assigned location. So, the main aim of optimizing this step is to store the load effectively and efficiently. You can take the help of warehousing software that can help you in allotting and managing warehouse space for each cargo that you receive for maximum space utilization. The software must also calculate the space in the warehouse for efficiently storing the product.
3. Picking Inventory
Picking is the process of collecting products from their allotted space to fulfill orders. It is the costliest step in the entire warehousing process and comprises almost 55% of the operating expense. Thus, optimizing this step can reduce the cost significantly. You can streamline this process to achieve higher efficiency and accuracy and reduce errors.
Picking is of two types:
- Primary: the primary picking is when the goods are directly sent to the staging or packing area for the finalization of the order and dispatching it. Thus, primary picking is also the last picking.
- Secondary: some orders are grouped before being sent to the staging and packing area. Thus, they are subject to a second picking process where other products are picked.
Once the orders are received, they are released in real-time or in a wave. Real-time is when the orders are released as soon as they are received. On the other hand, when orders are accumulated for a specific transport route or shipping time, it is called waves. Waves are released as per the discretion of the in-charge manager as per the criteria decided.
In a nutshell, the picking process can be discrete (picking one order at a time), clustered (picking multiple orders together), or batched (picking all the goods and then sorting them for a specific location). While some companies may use one of the types, some may employ all the types.

Optimization Tip
Introducing the right technologies is the best strategy to optimize the picking process. You can streamline the picking process by allowing warehousing workers to access the picking list wirelessly and accessing the system in real-time. You can also look forward to improving your warehousing layout, trying and choosing the right picking methodology, and utilizing different software that helps the workers execute the picking process efficiently.
4. Packing Orders
There are different ways you can pack the orders before shipping them. Packaging plays a crucial role in keeping the products safe and secure throughout the shipment and increases customer satisfaction. You can follow the following tips while packing products:
- Clearly mention all the ‘use-by’ and ‘best before’ dates in the packaging.
- Products picked up from different storage locations in the warehouse must be combined to ensure order completeness.
- You must pack all the goods as per their size, temperature, quantity, value, and hygiene.
- Make the products are future traceable by adding invoice numbers or document numbers to them.
Optimization Tip
Optimizing the packing process can be done by guiding the team who executes the task. A packing system that has all the necessary data related to the product dimensions and weight can help the team perform the task efficiently. Besides, you should also source the best packaging material that can keep the products safe and sound while shipping.
5. Dispatching Orders
The successful dispatch of the orders depends on the operation’s ability to keep the products packed and ready for departure before time. The manager, thus, requires forecasting and planning packing and dispatching well in advance. While packages that are ready in advance will fill up and jam the staging area, the late packages will delay deliveries.
Optimization Tip
Streamlining the tasks is crucial to optimize the shipping process. Allotting the right number of resources is also vital. A mobile application or software that shares the right information well in time can be really helpful.
6. Managing Returns
Managing returns are an important part of the entire warehousing process. Though it is a complex process, handling it well is important:
- Have a pre-determined return process describing what to do with the returned product – send them to the stock, destroy them, or return to the manufacturer.
- When customers initiate a return, they must be given a place where they can outline why they are returning the product.
- The returns must be trackable – their location through their invoice number or document number.
- Inventory must be timely updated when the goods are returned.
Optimization Tip
While many warehousing managements may not give the returning process its due importance, it can significantly affect the overall warehousing process. Having a system in place that describes what to do with the returned products and adding them automatically to the stock is vital.
The Final Words
The modern-day supply chain process is a bit complex. It includes a lot of activities, processes, and transactions. Using a pen and paper or managing on an excel sheet is not more of an option to efficiently manage warehousing operations. Investing in IT infrastructure is required to remain competitive in the market. Equally important is to optimize the warehousing process to ensure a smooth process and maximum customer satisfaction.
