Inventory is a non-liquid asset for a business that sells physical products. It must convert the liquid asset into cash by selling the inventory. How efficiently a company does that determines its profitability. Said that, the inventory carrying cost is an important metric to keep in the account.
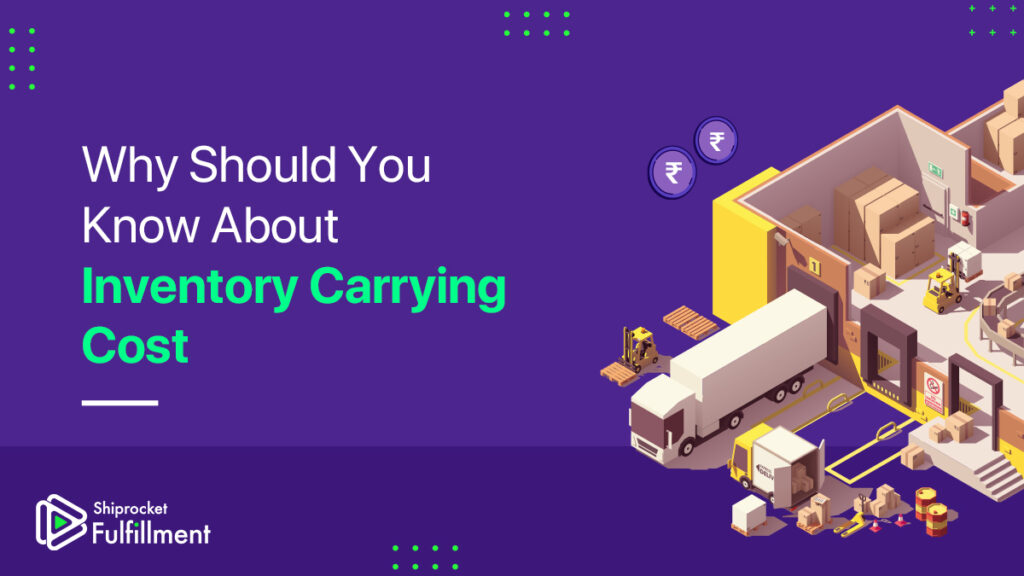
Inventory carrying cost is the amount a business spends on holding inventory – it includes the cost of owning, keeping, and storing inventory over a period of time. It simply is the expense of holding inventory before the orders are fulfilled.
An efficient inventory management process is required to keep inventory carrying costs minimum. With poor inventory management, carrying costs can increase, affecting most of the profit. Thus, implementing the best inventory control practices is essential to understand and measure the business’s carrying costs.
What Are Components of Carrying Cost?
Capital Costs
Capital costs account for the biggest portion of carrying costs. It includes the cost of purchasing raw material, inventory items, loan/financing fees, and loan interest. Money tied with inventory can affect cash flow. Thus, there can be a need for additional capital to run a business.
You need to forecast the inventory in advance and buy/restore inventory strategically. Also, you can negotiate with the supplier for a discount or lower inventory price.
Cost of Storing Inventory
Inventory storage cost is essentially the warehousing cost. It includes buying or renting a warehousing space; the cost paid for climate control and other utilities, security, and equipment if required.
While the cost is usually fixed if you own a warehousing space, the price depends on and fluctuates basis the usage and storage of inventory if you use a third-party logistics company. You can reimagine the warehouse layout from time to time to store different products and reduce storage costs.
Staff Cost
Staff cost is the labor cost that manages, arranges, and moves the inventory within the warehouse. They fulfill orders when you receive one. You can rearrange the inventory in the warehouse to cut labor costs. Like you can store inventory near packing stations. Or you can also automate some warehousing functions.
Inventory Service Costs
Many companies also insure the inventory. Flood or fire can destroy inventory. Thereby, insurance can cover the losses. However, the more inventory you have, the more the premiums will be. The inventory service costs include insurance premiums, hardware investments, taxes, and inventory management software fees.
Employing inventory management software can help you eliminate inefficiencies.
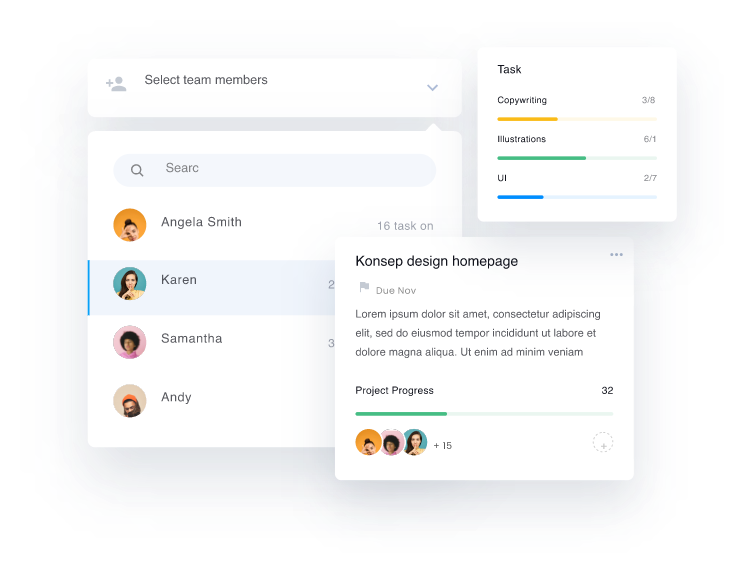
Obsolete Stock
Obsolete stock is the one that can be sold any longer. The reason can be the stock might have reached the end of its lifecycle. The products that become obsolete must be depreciated and written off the books. This can lead to a spike in the carrying cost.
The best way to eliminate obsolete inventory is by never overstocking. Otherwise, you will have to dispose it of. Or, when the stock is near the end of its lifecycle, you can offer discounts on it or donate it.
Also, if there are no regular checks, you might be holding obsolete inventory, leading to additional costs like warehousing. So. It is crucial to perform regular checks and dispose of the inventory before it becomes obsolete.
Inventory Handling
A product requires a number of touches – from putting it in the warehouse to printing shipping labels for it. All the money spent on this comes under material handling.
Administrative Costs
Administrative costs include a variety of expenses, like facility maintenance, cleaning, property taxes, and equipment and transportation depreciation. Generally, a company with more inventories incurs higher administrative costs because it needs a larger warehousing facility.
How to Calculate Inventory Carrying Cost?
To calculate carrying cost, divide the inventory on hold by the inventory value and multiply it by 100 to get the total inventory value percentage.
The total inventory on hold is the sum of all the components we have discussed above. And the inventory value is the cost of inventory available multiplied by the available stock.
So, the inventory carrying cost formula is:
Inventory Carrying Cost = Inventory Holding Cost/Total Value of Inventory X 100
With the carrying cost formula, you can calculate the quarter or annual carrying costs. It’s best to calculate carrying costs at regular intervals.
