- Stock Audits: What You Need to Know
- Inventory Audit Goals: What to Aim For
- Why Stock Audits Matter: Boosting Business Excellence
- Behind the Scenes: How Stock Audits Work
- Top Stock Audit Techniques: Making Every Count Count
- Tackling Stock Audit Hurdles: Challenges and Solutions
- eCommerce Advantages: Elevating Business with Stock Audits
- Fine-Tuning Your Inventory Insights: Best Practices
- Conclusion
Audits form a crucial part of the inventory management process for all businesses. It’s an extensive process that requires thorough planning to ensure accuracy in cross-checking financial records. Whether you run a retail store, a manufacturing facility, or an eCommerce business, managing your inventory is key to achieving efficiency in operations. If you don’t have proper control and oversight of your inventory, your inventory can become a costly headache for your business.
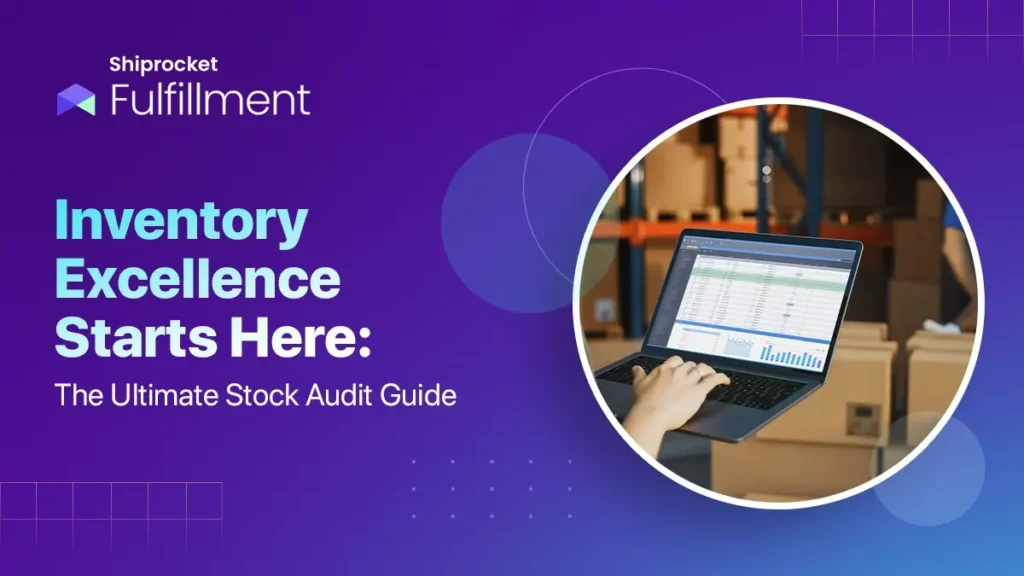
An inventory audit can help your business identify discrepancies in stock counting and ensure the accuracy of financial records against inventory records and physical counts.
Let’s explore stock audits in detail, tips to optimise your inventory audit process, why stock audits matter, and more.
Stock Audits: What You Need to Know
Stock audits are also referred to as inventory audits. The inventory audit procedure consists of validating or simply cross-checking your inventory’s financial records with the actual count of inventory. Internal or external auditing firms are employed to complete these processes.
Any auditing process can be mainly categorised as follows:
Internal Audit
These audits are carried out by an internal team. They assess your inventory management, process, assets, and inventory. Your business can nominate an auditor who reports to a higher authority or management. Internal audits are generally done to prepare the team for external audits. They are also conducted when the team is unsure about their inventory supplies or processes.
External Audit
A review that is strictly conducted with precision by an external agent or any non-affiliated accountant is called an external audit. These audits help your business attract investors and gain their trust.
Inventory Audit Goals: What to Aim For
The key objective of any inventory audit is to compare and identify discrepancies in financial inventory records and actual stock counts. As financial records are maintained internally, there is a possibility that they are incorrect, as humans are prone to making mistakes, omissions, and manipulations.
An inventory audit ensures that all these errors are eliminated, and the audit is completed accurately to present a fair picture of the business’s inventory state. Thus, stock auditing includes thorough verification processes and checks of the inventory not maintained in the company’s financial books.
The primary goals of any stock audit include:
Realisable value evaluation
The inventories are always listed on the general ledger. An auditor’s primary goal is to verify the value of the inventory listed. The auditing team also examines if the inventory has any damaged and low-quality items documented at their realisable value.
Verification of the physical existence of the stock
Cross-checking financial records with the physical count of the inventory is another goal of a stock audit. When such an audit is conducted, the counting process is checked to verify its efficiency. A sample of products is chosen to see if the physical counts match the financial records and vice versa.
Examining the accuracy of the operations
An auditor also ensures that the inventory counting method is accurate and that a statistical method is used for a sample of inventory.
Ownership rights
Evaluating if the business genuinely has ownership rights to the inventory documented in its books is another major goal of an auditor.
Why Stock Audits Matter: Boosting Business Excellence
Auditing every aspect of the inventory becomes crucial to achieving maximum efficiency. An inspection conducted on the inventory must validate the quantity of supply, its quality, and its condition to ensure that the stock’s worth is accurately determined. Here are the reasons why stock audits are important:
- Inventory audits are mandatory to check whether the actual number of units in the warehouse matches the actual financial records.
- The audit also reveals what materials are overstocked and which are understocked. It helps your business plan better while restocking.
- Auditing also helps you understand how to eliminate wasteful stock investments while balancing multiple business operations.
- It also helps you gain clarity and a clear image of all the stocks owned and recorded. When such counts are done correctly, it will present you with the knowledge of the business’s financial health. It helps you avoid inconsistencies in maintaining inventory records.
- A stock audit also helps you discover faults and errors with certain practices followed in your warehouses, either during packing or docking. It will help you find inefficiencies and discrepancies as well.
- Overstocking results in poor cash flow and losses, which can be avoided through accurate stock auditing. A stock audit must be conducted promptly to avoid such issues. Also, obsolete stock must be removed to ensure cost efficiency.
Behind the Scenes: How Stock Audits Work
Audits do not have a set-in-stone process. They vary based on the organisation and the type of stocks they hold. It also depends on the size of the inventory held by the company. However, here are the most common stages of an audit:
Stockpiling and forecasting demand
Running out of stock can be the most catastrophic occurrence during assembly and manufacturing processes. You do not want your company to run out of materials and halt supply chain processes. Although some smaller businesses can completely halt their processes for a day. However, it is a dangerous approach. Thus, it’s important to critically analyse your past data to forecast future demand.
Counting the physical items in the warehouse
Several techniques can be employed to continue this process. You can browse the items on the warehouse shelves individually. Or you can follow a cut-off analysis method to simplify the process. But it requires you to put your business on hold for a while, which is not an appropriate approach.
Trying the cycle count methodology can help you avoid halting your business process and can also help you assess your entire stock in one go. It might not be as accurate, but it is certainly less disruptive. A spot-check audit is another alternative. In this method, you check a few items in your inventory to identify any record-keeping errors. You can declare that your sources are current and the inventory is safe if you don’t find any errors.
Verifying your findings
Double-checking everything can be extremely tedious. But it’s crucial for stock auditing. Human error is a major issue, and when the project scope is larger, entrusting to a single source can cause errors. Hence, double-checking is mandatory. Trying different auditing tactics will help you find the most auditable strategy for your organisation.
There are other stock audit techniques you can use for stock audits. These include the following:
- Finished goods inventory analysis
- Freight cost analysis
- Overhead analysis
- Inventory in transit analysis
- High-value stock tests
- Direct labour analysis
- Inventory count reconciliation
Top Stock Audit Techniques: Making Every Count Count
Here are some of the best optimisation techniques for your organisation’s auditing processes:
Counting physical inventory
The most common way to sort this data is by using spreadsheets. You will count your items physically on all your inventory shelves and compare the results to the numbers in your books. This is the best way for those using a just-in-time inventory management system.
Numbering your inventory cycles
Like physical counting, cycle counting is a manual method of counting the number of products and comparing them with your books. Cycle counts are done periodically on a limited number of items. Hence, the frequent need for audits is eliminated.
Cutoff point analysis
Suspending all your inventory processes during your physical counting methodology is called cutoff point analysis. It minimises all the uncontrollable variables that tend to give errors.
Methods using analytics
A comparison of the turnover ratio and the gross margins and unit costs of the past year’s data allows you to identify any unreliable spikes and volatility. Hence, analytics can serve you in your auditing strategies.
Freight cost analysis
A study on how much you spend on your shipping and transportation and its lead time will help you optimise your supply chain. It also accounts for losses and damages that can occur during transport.
Product reconciliation
Analysing any issues discovered during inventory count to reconcile items can help you avoid record mistakes.
Tackling Stock Audit Hurdles: Challenges and Solutions
Here are some of the most common hurdles seen in stock auditing:
Inability to automate auditing processes
Most procedures must be done manually as they are too complicated to be automated. However, today, some activities can be performed with the help of certain specialised software. Investing in such systems can help you minimise manual errors.
Lack of real-time inventory picture
Stock verification must be done periodically in timely intervals as a real-time view can not be achieved during stock auditing. A weekly, monthly, or bi-monthly session might be excessive, but double-checking and verifying will help you minimise the number of audits required in a year.
Halts other operations
The auditing processes are extremely disruptive. They require you to shut down all processes until the completion of the audit. Planning ahead of time is the only solution to avoid such disruptions.
Managing stock is time-consuming
Managing stocks is extremely tedious, requiring great precision and labour. Thus, the simplest way to avoid this is to plan auditing times and allocate dates for them.
eCommerce Advantages: Elevating Business with Stock Audits
The benefits of stock auditing are many. Here are some of the benefits of inventory audits:
- Calculating gains: Calculating your earnings can be extremely simple due to audits. It presents the actual numbers without errors, making it easy to determine your gains.
- Accurate budgeting: As the true values are determined using auditing, it makes it easier to plan your allocation of funds for your activities. It makes the process more efficient.
- Keeping an eye out for inefficiencies: Identifying inefficiencies in the supply chain becomes easy with a stock audit. This also makes stocking easier with the true scenarios represented by the stock audit. All your processes can be optimised by analysing the audit results.
- Eliminating phantom inventory: Inventory that is unavailable when needed but present in the inventory is known as phantom inventory. It causes shelf issues, so auditing can help you avoid this completely.
Fine-Tuning Your Inventory Insights: Best Practices
Inventory audits address high-risk and high-value areas. They help you improve your efficiency, and here are some of the best methods to fine-tune your inventory insights:
- Asking as many questions as possible and avoiding making assumptions is the most effective method of learning inventory systems. Direct conversations with your inventory personnel will help you gain greater insights into the roots of problems and help you find solutions to your processes.
- Examining the storage facility’s accounting before entering can help you identify and determine where the largest stock values lie and its risks. Records and reconciliation records can also be examined to reveal what the management is having issues with and where your efforts can be focused.
- Most businesses tend to have a negative perception of an auditor. Cooperation is easily achieved when a business understands that an internal audit is to assist the organisation rather than shine a light on its faults.
Conclusion
Auditing the inventory is a crucial step for any business, regardless of its size and the industry in which it operates. A stock audit ensures your business’s financial records match against your inventory records. It helps you identify discrepancies in inventory counts, eventually minimising costs and increasing efficiency. A thorough and timely inventory review can help you avoid fraudulent situations and improve your inventory management processes while increasing profits.
There are some important documents you might need for a stock audit. These include:
A stock statement,
Provisional balance sheet,
Latest audited financial statements,
Stock insurance policy, if any,
Stock register,
Purchase and sale invoices,
Valuation method of closing inventory,
List of obsolete and non-moving inventory,
Debtors and creditors list, and more.
A stock audit report is a document that summarises the findings of a stock audit. The stock audit report highlights any discrepancies and identifies areas for improvement to minimise costs and losses.
Asset tags are applied to inventory. These are crucial during the physical verification process. These tags offer information in real-time since they feature built-in technology, including a barcode, QR code, RFID, etc. Each asset tag comes with a unique identification number. These identification numbers are recorded in accounting software, which helps you manage your inventory.
A stock audit is a more detailed process compared to stock verification. A stock audit is carried out by an internal or external auditor to verify the existence of goods in a stock. Stock verification is carried out by an independent person to verify the accuracy of inventory records.
A stock audit is done to verify the accuracy of inventory records a company maintains. An inventory count is often done to carry out a stock audit as a physical verification of the number of goods available in a business’s warehouse.