There are several industries that deal with perishables. The food industry is the biggest example that deals with products with low shelf lives. Businesses in the food industry can incur substantial losses as the raw materials and even finished goods expire or turn obsolete quickly. It is, therefore, very important for them to allot expiration dates to all product batches. It helps them push the near-expiration batch to the stores as fast as possible.
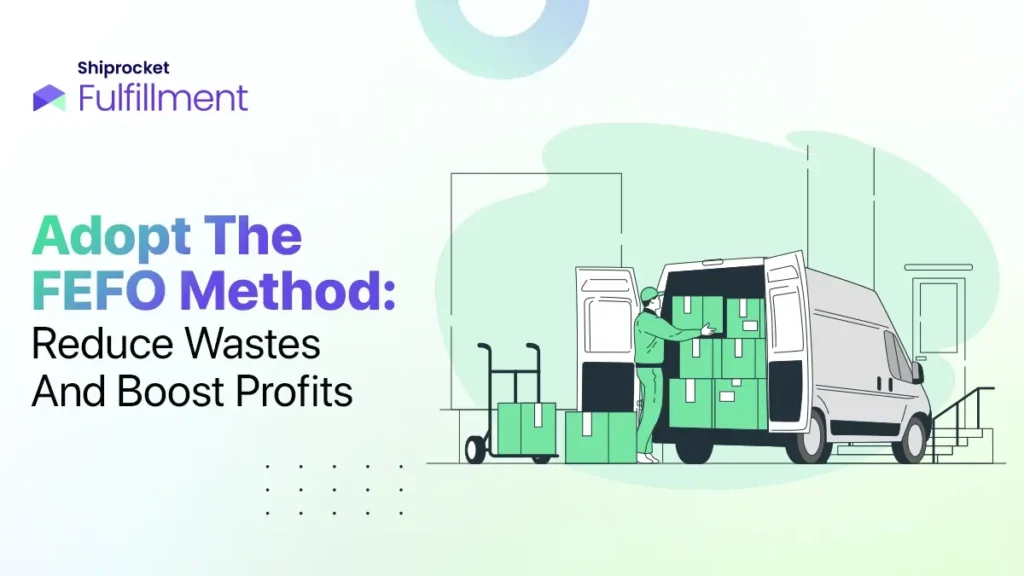
With the rapid development in technology, several automated solutions now make it possible to allow brands to pick products based on their expiration dates. It also enables them to set notifications for products nearing expiration and manage timelines accurately.
First Expired First Out, or simply FEFO, means exactly what it suggests. The FEFO method implies that products nearing their expiration dates are used or sold first. It is an important inventory management technique that’s primarily used for perishable items, including food, pharmaceuticals, and more.
Let’s explore the FEFO method in detail, how you can use it to minimise inventory losses, its benefits, and more.
Understanding FEFO
As mentioned above, the FEFO method implies that the product with the earliest expiration date is sent out first into the market for the consumers to buy. It enables businesses selling perishable items to minimise waste-related costs and added labour costs. It also helps ensure the products have a reasonable shelf life when they reach their consumer’s doorstep.
The FEFO method does not consider the warehouse’s manufacturing date or shelved date. It focuses solely on the expiration date. When you use this technique, you can avoid obsolescence of perishable goods.
The FEFO method has several advantages. They have a significant impact on the marketing strategies and brand reputation. Here is a list of benefits that the FEFO method brings into your supply chain processes:
- Customers check expiration dates before buying products. The FEFO method can help you provide the longest possible lead times before expiration, ensuring more products in a particular batch are sold.
- With all processes based on the FEFO method, the focus lies on the expiration dates. It allows you to plan your selling processes based not only on the expiration dates but also on the most convenient shipping method to sell your products as soon as possible.
- With the FEFO method, the warehouse staff becomes extremely aware of the expiration dates and also understands how long all the workflows in the process take. Hence, streamlining the backend workflows becomes easier.
- The FEFO method also ensures that inventory management processes pay extra attention to ensure that the products are fresh and fit for consumption.
The significance of the FEFO method stretches beyond the benefits mentioned above as well. This method also helps you:
- Create a fresh product cycle quickly and efficiently
- Minimise deadstock and losses that you might incur
- Integrate different processes harmoniously
- Eliminate time-consuming and labour-intensive processes
Calculating FEFO requires a few factors that are crucial for its accuracy. The prerequisites for calculating FEFO include its manufacturing date, use-by date, approximate shelf life duration, the quality of products, its barcoding strategies, and the adopted inventory management software.
Large businesses generally use barcodes to track batches of products. It enables the inventory management software to efficiently manage and pickup and shipping of products nearing the expiration date. Smaller businesses, on the other hand, might rely on manual processes to sort products nearing the expiration date.
Role of Barcoding in Enhancing the Supply Chain
Storage serialisation is simply termed barcoding. It makes it extremely easy to manage your inventory and also track products that are in the entire facility as well as those that are being used in the supply chain. By managing and handling the complete data of a product, a barcode helps you eliminate errors and discrepancies that can bleed across all the departments and functions along the supply chain.
With serialisation, your company can gain advantages like recognition, data implementation, and automatic identification of goods. It saves time and labour costs, boosting productivity.
The biggest advantage of barcoding in the supply chain is the control of quality and eliminating the expiration of products. A barcode stores a complete set of numbers and goods along with products’ expiration data that you can easily access to pick and ship product batches with the closest expiration dates.
Utilising FEFO to Minimise Inventory Loss
The inventory rotation by the FEFO method can help you reduce inventory losses and increase your profitability. By automating the process of FEFO, you can pick and ship out batches of products that are likely to expire very soon. The FEFO method relieves you of the worry of inventory wastage, both in terms of goods and costs.
In the food and pharmaceuticals industry or similar industries dealing in perishables, the FEFO method can help you use and sell all the products when they are still fresh, minimising the amount of wastage.
Advantages of FEFO Warehouse and Inventory Software
The FEFO method has a significant impact on your brand, either directly or indirectly. They positively affect your front-end and back-end processes while also pitching in on your marketing and branding strategies. Adopting warehouse and inventory software can further enhance the FEFO processes to avoid manual errors. Here are the most common benefits of using FEFO warehouse and inventory software:
- Enhanced confidence of the customer
When you buy products prone to expiration or perishing, checking the expiration date is a must. Some customers view products very close to the use-by date as unbuyable and then abandon the purchasing idea completely. Perishable items’ freshness is crucial to determining whether a customer is interested in buying a particular product, especially in low-shelf life cases.
You can sell items off shelves with the greatest possible lead time if you implement the FEFO method. Retail stores and distributors can gain access to the products well in advance. Hence, the end customers gain trust and confidence in your brand, which can help you establish a long-lasting relationship with them.
- Optimise the layout of your warehouse facility
Your inventory management processes must focus on the use-by date to ensure you incur as minimum losses as possible. You must ensure your warehouse follows a process that enables faster and easier picking of items that approach the use-by date. With the FEFO method, you can see how you can plan the process to ensure increased efficiency and reduced losses.
- Minimisation of the number of expired units
Every retailer wants to minimise the number of products not selling in their retail stores. These also include minimising obsolete and expired products. By adopting the FEFO warehouse and inventory software, you can ensure you sell goods based on the use-by date. It minimises the risk of having shelved goods that turn into unsellable goods or waste. It also eliminates the piling of stocks in your facility, reducing storage costs. Deadstock can also be taken care of with the FEFO method.
- Optimising the flow of items
A clear estimation of the total time taken to pick and ship a product is crucial. Hence, storage and warehouse personnel must have a clear understanding of the processes. It will help them understand the pace at which they must work while keeping the expiration date in mind. It will help you establish smooth and efficient workflows across your supply chain process and achieve optimum efficiency.
The FEFO inventory and warehouse method helps you automate your pick-up, packing, and transporting strategies by keeping the use-by date as the center of attention. It offers several benefits in optimising and integrating your backend inventory management processes. Eventually, it boosts your brand value and consumer satisfaction.
Conclusion
The expiration date can make or break a purchase for your customer. The longer the time between a customer purchases a good and when it expires, the better. With the FEFO method, you prioritise processes that bypass maximum wastage and minimise losses.
Exploring the FEFO method can help you gain control over your supply chain operations and integrate all your processes smoothly. Therefore, it helps you establish a more agile supply chain while avoiding deadstock. The FEFO method also ensures that you sell all your products well within the specified durations. It minimises the additional costs of over-storage and manual labour associated with dealing with spoiled inventory. Thus, the FEFO method can help you carry out your business operations smoothly and efficiently.
When you adopt the FIFO method of inventory valuation, you first sell the products you first bought. On the other hand, the FEFO method implies you first sell the products that are likely to expire very soon.
The FIFO, LIFO, and FEFO methods are different types of inventory valuation methods. The FIFO method implies the goods bought first are sold first. The LIFO method implies the goods bought last are sold first. Lastly, the FEFO method implies the products reaching their expiration dates soon are sold first.
The biggest drawback of the FEFO method is that the complete expiration details of all products can be difficult to track and manage. Adopting the FEFO method can also incur additional costs for the proper management of products expiring soon.